A successful injection
vowin.cn/en/News/news1251.html' target='_blank'>vowin.cn/' target='_blank'>molding project starts with the design of a product, and then the design of precision
plastic injection
molds. With the need for shorter lead times and better quality today nobody has time to get it wrong, so here’s how you can get it right.
Plastic injection molds can be complicated to get 100% right off the bat, especially if you’re trying to get it done from the other side of the world. You’ve heard all the rumors about bad quality and cost cutting when it comes to China, and you’re probably scared you will get substandard products if you do place an order with a mold maker in China.
But how hard is it to get it right?
If an injection mold is correctly designed with expert drawings explicitly specifying all the tolerances, including the materials, steel grades, hardness and surface finish requirements, then a plastic injection mold can be built anywhere in the world.
True some companies have had problems in the past
Cost, it all comes down to the bottom line! Companies focus on cutting cost so much that they stare themselves blind at the actual good quality moldsyou can produce in China.
So why all the hype, are the Chinese dishonest?
In any business, you need to dot your I’s and cross your T’s, and you can’t generalize and call an entire country dishonest. As unlikely as it may sound it all comes down to communication, more precisely the breakdown of communication.
China prides themselves on producing excellent quality at the best pricing in the world, but if you don’t specify exactly what you require out of a mold, what materials to be used and merely accept cheap pricing for what it is, you’re going to burn your fingers. As the old adage goes “buying cheap is buying expensive.”
1. Know Where to Start
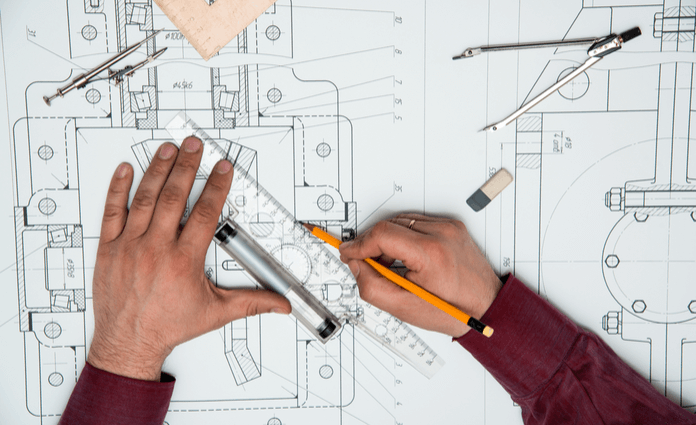
Firstly, you must understand that top quality molds are produced daily in China. But you need to follow a few “ground rules” to make sure you get top quality at the right price.
You must CLEARLY specify your requirements and only work with mold makers in China that you’ve vetted properly.
The drawings of your mold design need to be on point and drawn up by a professional, and there can be no margin for error. If you start your Chinese mold making communication and process with a well-defined drawing you’ve already won 90% of the battle.
Cost is key and it’s all about the bottom line, but business is business!
For a plastic mold making company to quote 50% less than that of its nearest competitor for the SAME plastic injection mold, they have to cut their costs to below 50% of their competitors. This is typically reflected (or not reflected at all) in material selection, surface finishes, material hardness, lack of precision grinding of mating surfaces, and lack of close tolerances in wall thickness on thin wall products.
All of these problems can be avoided by the clear statement of specifications at the RFQ stage. The problem with obtaining quotes from mold makers in China is that when rigorous specifications are required, the price differential between quality mold makers (irrespective of global location) becomes minimal. The total cost of ownership when outsourcing plastic injection molds should reflect all of the costs associated with testing and ultimately accepting a mold produced in a foreign country, and the additional precautions required to ensure that no technical errors are made because of language barriers.
There are a large variety of standard mold makers in China, and the most difficult thing is to choose the best fitting mold maker for a company from the onset. This can be a tedious process, and sometimes the results can be somewhat underwhelming.
Even though it’s relatively easy to find a trusted, well-known mold maker in Germany, UK, Japan or the US, finding a mold maker in China worth their salt (with reasonable pricing) is not as difficult as you might think.
But for now let’s move on to what you can do to ensure world-class molds, and keep them safe.
2. Make 100% Sure That You Own the Mold and Any Rights for That Mold
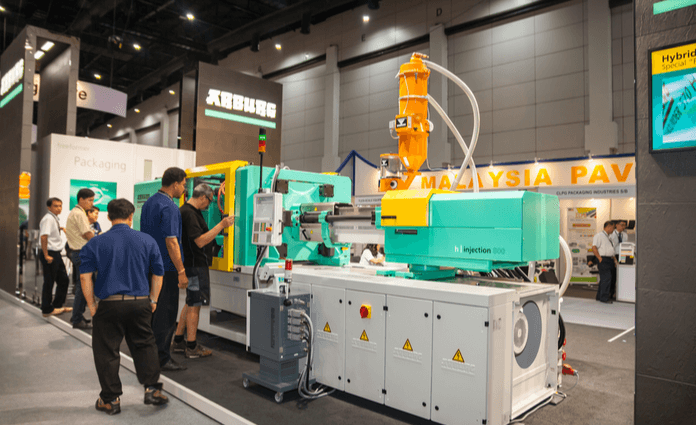
If you’re shipping the mold overseas, you will take possession of the mold, but still there are areas you need to be very clear on with your Chinese moldmakers, like complete ownership, IP, etc. However, if you’re producing with a factory in China it is critical you make sure that the mold makers understand that YOU own the physical mold.
Firstly – you need to make it clear to the manufacturer/factory in China can only use the molds for producing your products and that they can’t produce any products for a third party using your mold or mold designs.
Secondly – you need to make sure that if you want to move your mold at any point in time to a different factory, that the receiving facility will have the right to take possession of the molds and that you can freely move them to a new location.
Why would they try to keep your mold?
Chinese manufacturers have a strong incentive to keep your molds and prevent foreign buyers from moving to a new location or factory. In a lot of cases, the mold embodies most or all of the IP in the product.
With some products, the interior mechanism is based entirely on open source hardware. The exterior enclosure around the mechanism is, therefore, the p
rimary protectable IP for the product. The intellectual property lies entirely in the
molds used to manufacture the product case. The outside “appearance” of the enclosure then becomes the ID of the product, and if that “appearance” isn’t protected, you will own NOTHING at all in the IP of the product. Without that IP in the
mold protected, the Chinese factories can copy the product as they see fit.
On the other hand, in some products, the form embodies in the mold holds the entire value of the product. One example could be that of a single part used in an extremely complex engine, like that of a jet engine. After all the designing, engineering and testing is complete what will you be left with? A single part produced by casting into single or multiple molds.
In this instance, the molds embody the entire intellectual property for that part. In short, whoever owns or controls the IP in the molds is essentially in complete control of the product, so you can see why this is a crucial aspect of mold making in China.
What happens if the IP isn’t defined?
If NOBODY owns any of the IP in the molds, they are then effectively classified as an open source, which means nobody owns any of the IP in the moldsor for the product, which is a scary place to be. And the Chinese factories have figured this out which can make protecting your molds quite hard.
This means when you’re drawing up an agreement with the mold maker you can’t focus solely on ownership but have to consider the IP in the mold as well.
What Can You Do to Prevent Trouble Further On?
3. Your or a Trusted Third Party Should Be Present at the Mold Testing
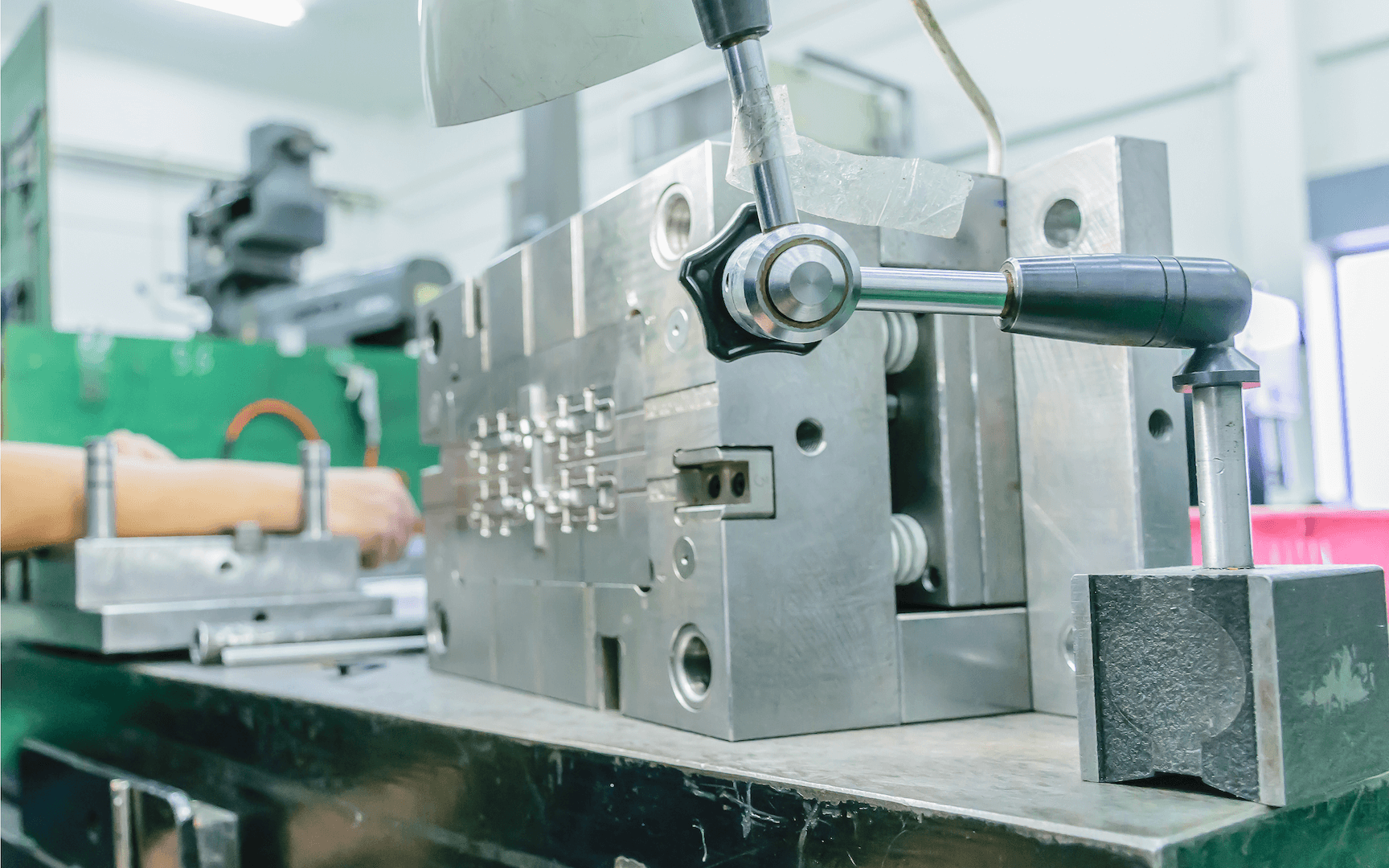
The proof of the pudding is in the eating!
Once the molds have been manufactured they have to be tested PROPERLY, reports filed, feedback is given on the outcome, and most important of all any faults or parameter fails needs to be rectified.
To do this, the mold is mounted onto adequately sized injection molding machines, set up for an optimized injection cycle, and launched for a limited production run with all the parameters of a full production intent operation.
This allows you to inspect the tools under real performance situations, fine tune its settings, and generate a complete report of findings including the points that need adjustment or improvement and tool modifications for a trouble-free operation that affords the mold a maximum lifespan.
It’s critical that yourself or a representative of your company be present and in most cases a third party QC company with a track record in experience to be present and advise on the outcomes of the mold testing.
You can NOT leave this in the hands of the manufacturer
The final steps in testing the mold can make a world of difference where the difference in success and failure is measured in micro-millimeters, and there’s no substitute for experience in this regard.
Make Sure You Request the Following from Your Mold Maker
-
Verifiable references
-
Origin of Steel with accompanying chemical analysis report
-
Overall Capital investment of the mold maker (this must be made available from manufacturers, if the capital investment is on the weak side, less than a few million, it will indicate a small time operation.) A company’s online presence can sometimes be misleading
-
Are they an OEM or are they the middle man?
-
Previous quality reports if available
-
Quality System guides
-
Case Studies of previous work
-
Capabilities – do they outsource or is everything done in-house
-
Capacity and lead time at the date of wanting to place your Purchase Order
We hope you find the information in this blog will set you on the path to source the best mold makers in China.
Do you have any questions about manufacturing molds in China? Any cautionary tales of your mold making stories in China? Please feel free to leave a comment below
One last note from the horse’s mouth:
”I set up and managed a plastic injection mold and precision mold component manufacturing company in Shenzhen for four years. There are many reasons why it is difficult to get a quality product built there. While we were able to train our Chinese makers to do US quality work to ‘tenths’, it was not a quick and easy process and we had to be continuously vigilant as they would slip into the old ways if we were not watching. My simple advice in every circumstance would be to prove the product by complete inspection before it leaves China.” – “Huber”